Unit-01: Study Notes for DS369
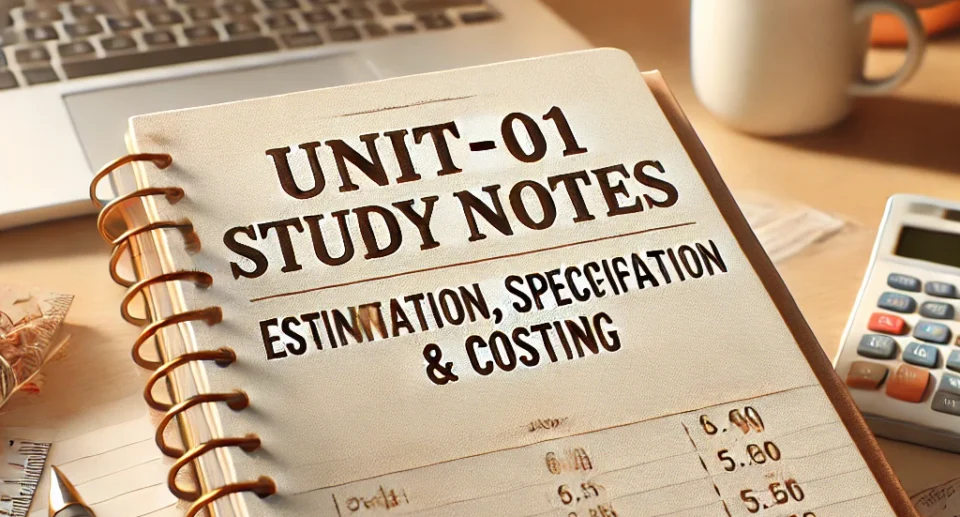
What is Specification?
Specification is a detailed and precise description of materials, workmanship, quality standards, and execution methods used in a construction or interior design project. It serves as a guideline for contractors, designers, and engineers to ensure the project meets the required standards.
Key Features of Specification
- ◈ Defines the quality, quantity, and type of materials to be used.
- ◈ Provides instructions on the execution process and finishing details.
- ◈ Ensures consistency, accuracy, and compliance with industry standards.
- ◈ Helps in cost estimation, procurement, and contract documentation.
Types of Specification
Specifications are categorized based on their level of detail, purpose, and method of description.
General Specification
-
- ◈ Gives an overview without specific technical details.
- ◈ Covers the type of materials, quality level, and scope of work.
- ◈ Used in preliminary project stages and client discussions.
Table 1 General Specification (Sample)
S. No. | Item | Specification |
1 | Walls & Wall Finishes | Brick/block masonry with cement mortar (1:4) 12mm thick cement plaster with a smooth finish Two coats of acrylic emulsion paint over primer |
2 | Flooring | Vitrified tiles of 600×600 mm, anti-skid for wet areas Laid on a cement mortar bed with tile adhesive Cement-based grout matching tile color |
3 | Ceiling | POP/Gypsum board false ceiling Painted with water-based emulsion in an approved shade |
4 | Doors & Windows | Solid wood (Teak/Mahogany) or engineered wood (MDF/Plywood) Powder-coated aluminum or UPVC with clear glass panels Stainless steel hinges, locks, and handles |
5 | Furniture | Marine plywood with laminate finish PVC edge banding for durability High-quality fabric or leatherette, fire-resistant |
6 | Electrical & Lighting | Concealed copper wiring in PVC conduit Modular switches, LED light fittings Adequate provisions for lighting, fans, and sockets |
7 | Plumbing & Sanitary Fittings | CPVC for hot & cold water supply Ceramic washbasins and water closets (Jaquar/Hindware or equivalent) Stainless steel/brass with chrome-plated finish |
8 | Sustainability Considerations | Use of low-VOC paints for better air quality LED lighting for reduced power consumption Low-flow faucets and dual-flush toilets |
Detailed Specification
-
- ◈ Includes exact materials, measurements, workmanship, testing standards, and execution methods.
- ◈ Used for contract documents, tendering, and execution on-site.
- ◈ Example: “The wooden doors shall be made of 32mm thick solid teakwood, polished with three coats of PU varnish, and fitted with stainless steel hinges and handles.”
Table 2 Detailed Specification (Sample)
S. No. | Item | Detailed Specification |
1 | Walls & Wall Finishes | Material: Brick/block masonry with cement mortar (1:4). Plaster: 12mm thick cement plaster with a smooth finish. Finish: Apply one coat of primer followed by two coats of acrylic emulsion paint. Paint Brand: Asian Paints / Dulux or equivalent. |
2 | Flooring | Material: Vitrified tiles, size 600×600 mm, anti-skid tiles for wet areas. Tile Fixing: Laid on a 20mm thick cement mortar bed with tile adhesive. Grouting: Tile joints shall be filled with epoxy grout in matching color. Tile Brand: Kajaria / Somany / Johnson or equivalent. |
3 | Ceiling | Material: Gypsum board (12mm thick) with galvanized iron (GI) framework. Finish: Surface to be joint-treated and painted with water-based emulsion. Installation: False ceiling to be suspended from MS framework using anchor fasteners. Gypsum Board Brand: Gyproc / USG Boral or equivalent. |
4 | Doors & Windows | Doors: Made of solid teakwood with factory-pressed laminate finish. Windows: Powder-coated aluminum frame with 6mm clear toughened glass. Hardware: SS 304-grade hinges, locks, and handles. Finish: Wooden surfaces to have PU polish, metal frames to be powder-coated. |
5 | Furniture | Material: 19mm BWP (Boiling Water Proof) Marine Plywood. Finish: High-pressure laminate on visible surfaces, PVC edge banding. Upholstery: High-quality fire-retardant fabric or leatherette. Joinery: Dowel jointing with concealed screws and glue bonding. Furniture Brand: Greenply / Century Ply or equivalent. |
6 | Electrical & Lighting | Wiring: FRLS (Fire Retardant Low Smoke) copper wiring in PVC conduit. Switches: Modular switches with a minimum 10A rating. Lighting: LED recessed downlights for general lighting. Sockets: 5A and 15A power sockets as per electrical layout. Switches Brand: Legrand / Schneider / Havells or equivalent. |
7 | Plumbing & Sanitary Fittings | Pipes: CPVC pipes for water supply, UPVC pipes for drainage. Sanitary Fixtures: Wall-mounted ceramic washbasin, dual-flush WC. Faucets: Chrome-plated brass faucets with quarter-turn operation. Accessories: Towel rack, soap dish, mirror with LED backlight. Sanitary Brand: Jaquar / Hindware / Kohler or equivalent. |
8 | Sustainability Considerations | Paints: Low-VOC acrylic emulsion for better indoor air quality. Energy: LED lighting with automatic occupancy sensors. Water Saving: Dual flush cisterns and low-flow faucets. Eco-Friendly Materials: Bamboo, recycled wood panels, cork flooring. Compliance: IGBC / LEED certification guidelines to be followed. |
Importance of Specification
Specifications are critical in interior design and construction because they ensure clarity, quality control, and proper project execution.
Ensuring Quality & Standardization
- ◈ Defines minimum quality standards for materials and workmanship.
- ◈ Avoids use of substandard materials by contractors.
- ◈ Ensures durability, functionality, and safety.
Cost Control & Budget Planning
- ◈ Prevents unnecessary expenses due to material changes or rework.
- ◈ Helps in estimating accurate project costs before execution.
- ◈ Ensures fair pricing and transparency in procurement and tendering.
Avoiding Disputes & Legal Clarity
- ◈ Acts as legal documentation between clients, contractors, and vendors.
- ◈ Helps in resolving contract disputes over material selection and workmanship.
- ◈ Reduces the chances of misinterpretation or errors during construction.
Time Management & Project Efficiency
- ◈ Provides clear guidelines to contractors, avoiding delays and confusion.
- ◈ Helps in scheduling material procurement and installation processes.
- ◈ Ensures smooth workflow and coordination among different teams.
Safety & Compliance
- ◈ Ensures that the materials and construction methods meet fire safety, health, and environmental standards.
- ◈ Helps in designing ergonomic and hazard-free interiors.
Enhancing Aesthetic Appeal
- ◈ Ensures the final product aligns with the design intent and client expectations.
- ◈ Helps in achieving a consistent and harmonious interior theme.
Panelling
Panelling in interior design refers to the process of covering walls, ceilings, or other surfaces with decorative or functional panels. These panels can be made from wood, MDF, PVC, glass, metal, fabric, or other materials to enhance the aesthetic appeal, durability, and insulation of a space.
Purpose of Panelling
- ◈ Aesthetic Enhancement – Adds texture, patterns, and depth to walls.
- ◈ Wall Protection – Shields walls from damage, moisture, and stains.
- ◈ Acoustic Insulation – Reduces noise and improves soundproofing.
- ◈ Thermal Insulation – Helps regulate indoor temperatures.
- ◈ Concealment – Hides electrical wiring, plumbing, or uneven surfaces.
- ◈ Customization – Allows for creative and personalized design styles.
Types of Panelling
- ◈ Wooden Panelling – Plywood, MDF, Veneer, Laminate
- ◈ Metal Panelling – Aluminium, Stainless Steel
- ◈ Glass Panelling – Frosted, Toughened, Stained
- ◈ Fabric Panelling – Acoustic Panels
- ◈ PVC & UPVC Panelling – Lightweight & waterproof
Detailed specification for Wooden Panelling
Wooden panelling is a popular interior finishing material used for wall cladding, decorative finishes, and insulation. Plywood is a commonly used material for wooden panelling due to its strength, durability, and versatility. It enhances the aesthetic appeal of interiors while providing thermal and acoustic insulation.
Table 4 Detailed Specifications for Wooden Panelling
S. No. | Item | Specification |
1 | Material | Plywood is made from multiple layers of wood veneers bonded with waterproof adhesives. BWP (Boiling Water Proof) grade plywood is recommended for high-moisture areas. Must conform to IS 303:1989 for standard quality and IS 5509:2000 for fire-resistant applications. |
2 | Thickness | Available in 6mm, 9mm, 12mm, 18mm, and 25mm. – 6mm – 9mm: Suitable for decorative lightweight panels. – 12mm – 18mm: Used for wall paneling and partitions. – 25mm: Heavy-duty applications and soundproof paneling. |
3 | Finish | – Laminate Finish: Scratch-resistant and durable. – Veneer Finish: Provides a natural wood grain look. – Painted Finish: For custom colors and modern interiors. – PVC Edge Banding: Protects edges and enhances durability. |
4 | Installation Method | – Panels are fixed onto a wooden framework (Salwood/Kailwood battens). – Secured with stainless steel screws or high-strength adhesives. – Installed with a 2mm shadow gap for expansion and contraction. – Joints are filled with wood filler and sanded smooth before finishing. |
5 | Maintenance | – Clean with a dry or damp microfiber cloth to remove dust. – Avoid direct exposure to water to prevent warping. – Periodic polishing or re-laminating helps maintain appearance. – Use mild cleaners; avoid harsh chemicals. |
6 | Fire & Moisture Resistance | – Fire Retardant Plywood (IS 5509:2000) is recommended for public and commercial buildings. – Waterproof plywood (BWP/BWR grade) should be used in kitchens, bathrooms, and humid areas. |
7 | Sustainability | – FSC-certified plywood ensures environmentally responsible sourcing. – Low VOC adhesives help maintain indoor air quality. – Plywood is biodegradable and recyclable, making it an eco-friendly material. |
Partition walls
Partitions are non-load-bearing walls used to divide spaces in residential, commercial, and industrial interiors. They can be fixed or movable and made from various materials, such as gypsum, glass, metal, wood, or PVC. Below is a detailed specification format for writing partition specifications.
Types of Partition Walls
- ◈ Gypsum Board Partitions – Made from gypsum sheets on a metal frame, used for lightweight partitions.
- ◈ Glass Partitions – Toughened, laminated, or frosted glass, used for modern office and retail spaces.
- ◈ Wooden Partitions – Plywood, MDF, or solid wood, for decorative and functional partitions.
- ◈ Metal Partitions – Aluminium or steel, used for industrial settings.
- ◈ Concrete & Brick Partitions – Cement blocks or bricks, used for permanent partitions.
- ◈ PVC Partitions – Lightweight, waterproof, used in wet areas like bathrooms.
Table 4 Detailed Specifications for Partition Walls
S. No. | Item | Specification |
1 | Material | – Plywood Partitions: Made from BWP/BWR grade plywood, conforming to IS 303:1989 for durability and moisture resistance. – MDF (Medium Density Fiberboard): Suitable for smooth finishes and decorative applications. – Solid Wood: Teak, Mahogany, or Oak wood for high-end decorative partitions. – Laminated Board: Particle board or MDF with a laminate or veneer finish. |
2 | Thickness | – 12mm – 18mm: Used for lightweight partitions and decorative panels. – 18mm – 25mm: Suitable for structural wooden partitions with framing. – Above 25mm: Used for acoustic and high-impact partitions. |
3 | Finish | – Laminated Finish: Scratch-resistant and available in multiple textures and colors. – Veneer Finish: Provides a natural wood grain look with polish. – Painted Finish: Customizable colors for modern interiors. – PVC Edge Banding: Used to protect the edges from wear and tear. |
4 | Fixing & Installation | – Framework: Fixed on a timber or aluminum framework with spacing of 600mm to 900mm centers. – Joints & Fastening: Secured using stainless steel screws, wood adhesives, or nails. – Edge Treatment: All joints to be sealed with wood putty or joint sealant for a seamless finish. – Support: Partitions extending to the ceiling must be braced with a wooden or metal frame for stability. |
5 | Acoustic & Thermal Insulation | – Soundproof Wooden Partitions: Filled with acoustic wool or foam panels for noise reduction. – Thermal Insulation: Insulated with cork or fiberboard to maintain indoor temperature. |
6 | Maintenance | – Regular dusting and wiping with a dry or slightly damp cloth. – Periodic polishing or repainting to maintain appearance. – Avoid exposure to excessive moisture to prevent warping. |
7 | Fire & Moisture Resistance | – Fire-Retardant Partitions: Fire-resistant plywood (IS 5509:2000) is recommended. – Moisture-Resistant Partitions: BWP/BWR plywood or MDF should be used in bathrooms and kitchens. |
8 | Sustainability | – FSC-certified wood should be used to ensure responsible sourcing. – Low VOC adhesives and paints should be used to reduce indoor pollution. – Recyclable wood materials for eco-friendly construction. |
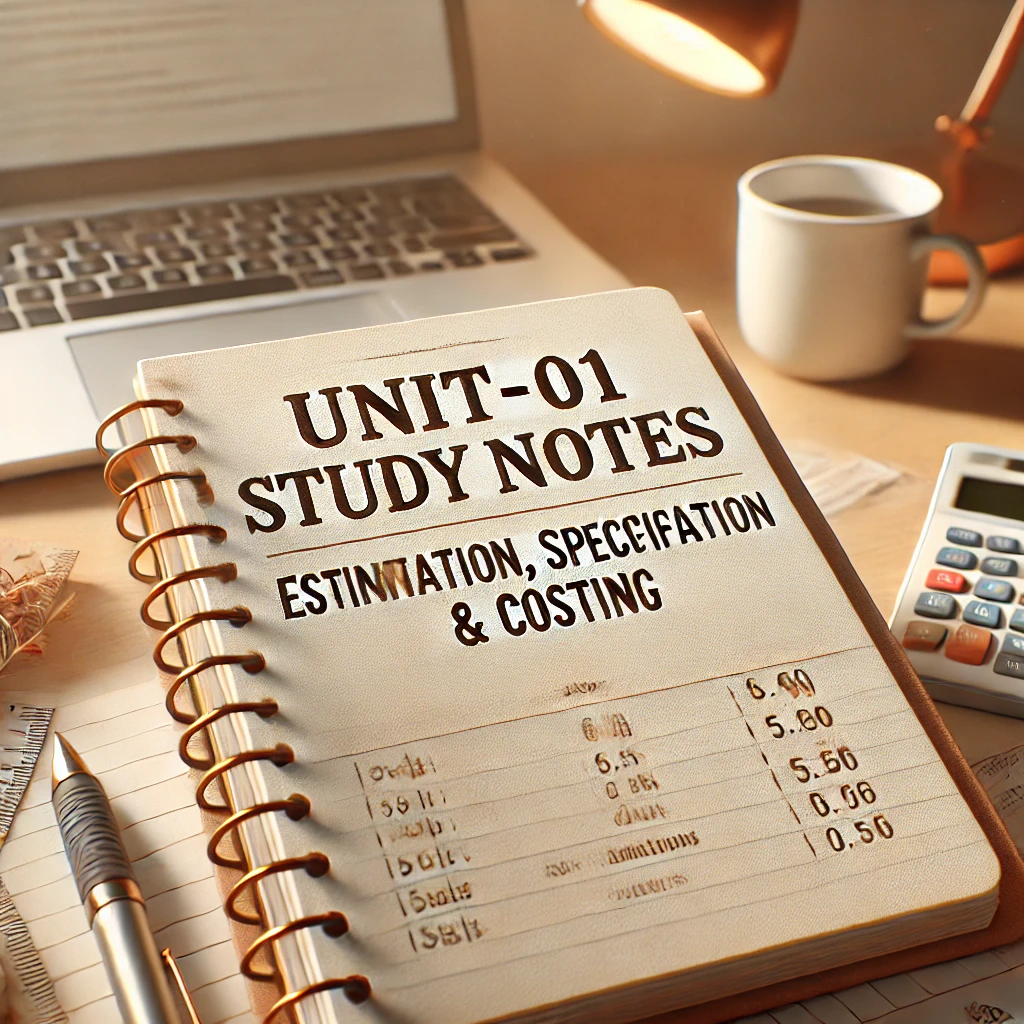
False Ceiling
A false ceiling, also known as a dropped ceiling, suspended ceiling, or secondary ceiling, is a secondary layer installed below the original ceiling of a room. It is commonly used in residential, commercial, and industrial buildings for aesthetic, functional, and structural purposes.
Purpose of False Ceilings
- ◈ Aesthetic Enhancement – Hides structural elements, wiring, and ductwork while adding a stylish look.
- ◈ Thermal Insulation – Helps maintain indoor temperature by reducing heat absorption.
- ◈ Acoustic Insulation – Reduces noise levels and improves soundproofing.
- ◈ Lighting Integration – Allows for recessed lighting, LED strips, and spotlights.
- ◈ Concealment of Services – Hides electrical wiring, plumbing, HVAC ducts, and fire sprinkler systems.
- ◈ Fire Resistance – Some materials offer fireproofing benefits, enhancing safety.
- ◈ Moisture & Weather Protection – Prevents dampness and reduces the impact of temperature changes.
Table 5 Detailed Specifications for False Ceiling
S. No. | Item | Specification |
1 | Material | – Gypsum board should conform to IS 2095:2011 for standard gypsum plasterboards. – Thickness options: 9mm, 12.5mm, and 15mm (commonly 12.5mm for standard ceilings). – Moisture-resistant gypsum boards (MR) for high-humidity areas like bathrooms and kitchens. – Fire-rated gypsum boards should be used in fire-prone areas. |
2 | Framework | – Ceiling framework should be made of galvanized iron (GI) channels conforming to IS 277:2003. – Primary channels (main runners) spaced at 1200mm centers. – Secondary channels (cross members) at 600mm centers for added support. |
3 | Fixing & Installation | – Gypsum boards should be screwed to the GI framework using self-tapping drywall screws at 200mm intervals. – Joints should be sealed with joint tape and jointing compound, then sanded for a smooth finish. – Expansion gap of 2-3mm should be left between boards to accommodate movement. |
4 | Finish | – Surface to be primed and painted with acrylic emulsion paint. – Can be finished with laminates, wallpaper, or textured paints for aesthetic enhancement. – Coving or cornices may be added for decorative appeal. |
5 | Lighting & Electrical Provisions | – Recessed lights, LED strip lights, and ceiling fans must have pre-cut openings in the gypsum board. – Electrical conduits should be concealed within the ceiling cavity for a neat appearance. |
6 | Acoustic & Thermal Properties | – Acoustic insulation can be improved by adding mineral wool or rock wool above the ceiling. – Enhances thermal insulation by reducing heat transfer between floors. |
7 | Fire & Moisture Resistance | – Fire-rated gypsum boards (with glass fiber reinforcement) should be used for fire-resistant ceilings. – Moisture-resistant boards should be used in bathrooms and kitchens to prevent dampness. |
8 | Maintenance | – Regular dusting and cleaning with a dry cloth. – Avoid excessive moisture exposure to prevent sagging. – Repair any cracks using joint compound and repainting. |
9 | Sustainability | – Gypsum board is eco-friendly, recyclable, and non-toxic. – Use low-VOC paints and adhesives to maintain indoor air quality. |
Flooring and Floor Covering
Flooring refers to the permanent surface finish applied to the structural floor of a building. It is designed to provide durability, functionality, and aesthetic appeal. The choice of flooring depends on usage, foot traffic, maintenance, and environmental factors.
Floor covering, on the other hand, refers to a removable layer placed over the flooring to enhance comfort, insulation, and design. Examples include carpets, rugs, and mats.
Importance of Flooring and Floor Covering
- ◈ Structural Strength – Provides a stable walking surface.
- ◈ Aesthetic Appeal – Enhances interior design with various textures and finishes.
- ◈ Durability & Maintenance – Resistant to wear, moisture, and impact.
- ◈ Thermal & Acoustic Insulation – Helps in noise reduction and temperature control.
- ◈ Safety – non-slip surfaces help prevent accidents.
Table 6 Specification for Tiles Flooring – Vitrified
S. No. | Item | Specification |
1 | Material | – Vitrified tiles made from a mixture of clay, silica, quartz, and feldspar. – Manufactured under high temperature and pressure, making them dense, non-porous, and highly durable. – Must conform to IS 15622:2017 for standard ceramic and vitrified tiles. |
2 | Tile Size & Thickness | – Standard sizes: 600×600mm, 800×800mm, 1000×1000mm, 1200×600mm (or as per project requirements). – Thickness: 8mm to 12mm depending on application. |
3 | Finish & Surface Treatment | – Available in Glossy, Matte, Satin, Rustic, and High Gloss finishes. – Polished vitrified tiles (PVT) have a high-gloss surface for luxury interiors. – Double charged vitrified tiles (DCVT) have a thicker wear layer for high traffic areas. – Full-body vitrified tiles have uniform color throughout for better wear resistance. |
4 | Fixing & Installation | – Surface must be levelled, cleaned, and free from dust before tile laying. – Tiles to be fixed using cement-based tile adhesive (C2 type, IS 15477:2019). – Tile joints to be filled with epoxy or polymer-based grout for a seamless finish. – Expansion joints must be provided at every 4-6 meters for structural movement. |
5 | Slip Resistance & Safety | – Matte or textured tiles to be used in wet areas such as bathrooms and kitchens. – Anti-skid tiles with R9 to R13 slip resistance rating recommended for safety. |
6 | Water Absorption & Stain Resistance | – Water absorption: Less than 0.5% (ISO 10545-3 standard). – Highly stain-resistant and easy to clean with mild detergent. |
7 | Maintenance & Durability | – Daily cleaning with a damp mop and mild cleaners recommended. – Avoid acidic or abrasive cleaners to maintain surface shine. – Periodic polishing may be required for high-gloss vitrified tiles. |
8 | Fire & Heat Resistance | – Fireproof and heat-resistant material, making it safe for commercial and residential applications. |
9 | Sustainability & Eco-friendliness | – Manufactured using eco-friendly materials with minimal wastage. – Recyclable and low carbon footprint in production. |
Furniture & Finishing Materials in Interior Design
Furniture and finishing materials play a vital role in interior design, offering functionality, aesthetics, comfort, and durability. Proper selection of materials ensures longevity, ease of maintenance, and sustainability in furniture design.
Importance of Furniture & Finishing Materials
- ◈ Functionality – Ensures furniture meets user needs (storage, seating, work surfaces).
- ◈ Durability – Long-lasting materials reduce maintenance costs.
- ◈ Aesthetic Appeal – Enhances interior design through colors, textures, and finishes.
- ◈ Sustainability – Eco-friendly materials contribute to a green environment.
- ◈ Maintenance & Hygiene – Easy-to-clean materials improve indoor air quality.
Table 7 Types of Furniture Materials
Type | Material Used | Key Features & Uses |
Wood | Teak, Mahogany, Pine, Oak | Strong, natural look, durable, used for tables, chairs, and cabinets. |
Engineered Wood | Plywood, MDF, Particle Board | Cost-effective, smooth finish, used for paneling and modular furniture. |
Metal | Steel, Aluminum, Wrought Iron | Sturdy, industrial look, used for bed frames, chairs, and office furniture. |
Plastic & Acrylic | Polycarbonate, ABS, Acrylic | Lightweight, waterproof, used in modern and outdoor furniture. |
Glass | Toughened, Frosted, Laminated Glass | Transparent, decorative, used for tables, cabinets, and partitions. |
Upholstery Materials | Leather, Synthetic, Fabric | Adds comfort, available in various textures and colors. |
Table 8 Types of Finishing Materials
Type | Material Used | Key Features & Uses |
Laminates | Decorative Laminates, High-Pressure Laminates (HPL) | Scratch-resistant, easy to clean, used for tabletops, cabinets, and wardrobes. |
Veneers | Natural & Engineered Veneers | Provides a premium wood-like appearance, used in high-end furniture. |
Paints & Polishes | PU Polish, Melamine, Duco, Enamel | Protects wood, enhances aesthetics, available in glossy, matte, or textured finishes. |
Glass Finishes | Etched, Frosted, Tinted, Stained Glass | Used for decorative elements, partitions, and tabletops. |
Acrylic Finishes | High Gloss, Matte Acrylic Sheets | Durable, modern finish, often used in modular kitchens and furniture. |
Applications of Furniture & Finishing Materials
- ◈ Residential Spaces – Sofas, beds, dining tables, wardrobes, and modular kitchen units.
- ◈ Commercial Offices – Workstations, conference tables, storage units, ergonomic chairs.
- ◈ Hotels & Restaurants – Upholstered seating, decorative partitions, bar counters.
- ◈ Outdoor & Public Spaces – Weatherproof plastic, metal, and treated wood furniture.
Table 9 Specification for Furniture & Finishing Materials – Wood (Teak)
S. No. | Item | Specification |
1 | Material | – Teak wood (Tectona grandis) is a high-quality hardwood known for its durability, strength, and natural resistance to moisture and pests. – Should be seasoned and kiln-dried to reduce moisture content below 12% for stability. – Conforms to IS 4021:1995 for furniture-grade teak wood. |
2 | Grades & Types | – Burmese Teak – Premium quality, high oil content, used for luxury furniture. – Indian Teak – Moderately high strength, suitable for general furniture. – African & Indonesian Teak – Cost-effective, slightly lower density, used for budget-friendly projects. |
3 | Thickness & Dimensions | – Available in planks and boards ranging from 12mm to 50mm thick. – Standard plank sizes: 4ft x 8ft, 6ft x 3ft, or custom-cut as per design. |
4 | Finish & Surface Treatment | – Natural Teak Finish – Oiled to enhance wood grain. – PU Polish (Polyurethane) – Provides a protective glossy/matte finish. – Melamine Polish – Enhances durability and shine. – Wax Finish – Preserves natural texture with a mild sheen. |
5 | Fixing & Joinery | – Joinery methods include dowel joints, mortise and tenon joints, and finger joints for high strength. – Screws and nails should be stainless steel or brass to prevent rusting. – Wood glue should be water-resistant (WBP grade) for durability. |
6 | Application in Furniture | – Used for tables, chairs, cabinets, beds, doors, and window frames due to its high strength. – Suitable for indoor and outdoor furniture because of its moisture resistance. |
7 | Moisture & Pest Resistance | – Naturally resistant to termites, fungi, and weather changes. – Can be treated with wood preservatives (boric acid or copper-based chemicals) for additional protection. |
8 | Maintenance & Cleaning | – Clean with a dry or slightly damp cloth; avoid excessive water exposure. – Periodic re-polishing recommended every 3-5 years to maintain shine and durability. – Avoid direct sunlight exposure to prevent color fading. |
9 | Sustainability & Eco-Friendliness | – FSC-certified teak wood should be used for environmentally responsible sourcing. – Reclaimed teak wood is a sustainable alternative. – Low-VOC finishes recommended for eco-friendly interiors. |
Modern Materials
Modern materials are innovative, sustainable, and technologically advanced materials used in architecture, interior design, and construction. These materials enhance performance, reduce environmental impact, and improve aesthetics and functionality. Modern materials integrate smart technology, eco-friendliness, and advanced coatings to meet evolving industry demands.
Need for Modern Materials
- ◈ Sustainability – Reduce carbon footprint and use renewable resources.
- ◈ Innovation – Offer new functionalities such as self-healing, energy efficiency, and recyclability.
- ◈ Technology Integration – Smart materials with thermal, acoustic, and interactive properties for intelligent spaces.
- ◈ Aesthetics & Functionality – Enhance design flexibility, durability, and user comfort.
Table 10. Examples of Modern Materials
Material | Type | Key Features & Uses |
Smart Glass | Electrochromic, Thermochromic | Changes transparency with electric current or temperature, used in windows and partitions. |
Bamboo & Cork | Eco-friendly, Renewable | Used for flooring, wall panels, and furniture; sustainable and biodegradable. |
Recycled & Upcycled Materials | Plastic, Wood, Metal | Repurposed from waste materials, reducing environmental impact in furniture and construction. |
Acrylic Solid Surfaces | Corian, Hi-Macs | Seamless, non-porous, stain-resistant surfaces used in countertops, bathrooms, and furniture. |
Nano-coating Materials | Anti-bacterial, Anti-dust | Used for self-cleaning surfaces, high durability, and antimicrobial properties. |
Table 11. Standard Format for Writing Specifications for Modern Materials
S. No. | Specification Category | Details |
1 | Material | Type and composition of the material (e.g., Smart Glass – Electrochromic with thin-film coating). |
2 | Composition | Primary ingredients, recycled content, or additives enhancing performance (e.g., Nano-coating – Titanium dioxide particles for self-cleaning properties). |
3 | Size & Dimensions | Standard sizes, thickness, and custom variations (e.g., Acrylic Solid Surfaces – 12mm thick, available in 3ft x 8ft sheets). |
4 | Properties | Strength, flexibility, durability, fire resistance, water resistance, and environmental impact. |
5 | Installation Method | Fixing techniques, adhesive requirements, electrical integration (e.g., Smart Glass requires electrical wiring for dimming functions). |
6 | Maintenance & Durability | Cleaning procedures, lifespan, and recommended protective coatings (e.g., Nano-coating requires periodic UV exposure for activation). |